Laser Cladding is a process for making (or repairing) metalic components that are generally larger in size than those made using selective laser melting. The metal to be “added” can take the form of fine powder that is carefully blown into the focus of a laser beam, or it can be in the form of a thin wire which is slowly fed into the focus of a laser beam. The assembly of the laser focusing optics and the metal to be added is termed a cladding head. By moving the cladding head in 3, 4 or even 5 axes, large and complex component geometries can be realised.
Beam shaping can play a crucial role in optimizing laser additive manufacturing process and enhancing benefits of both SLM and laser cladding. By tailoring the laser beam’s shape, intensity distribution, and size, beam shaping techniques offer several advantages:
- Improved Surface Quality: Beam shaping allows for precise control over the energy distribution, resulting in enhanced surface finish and improved part quality. It helps to minimize surface roughness, porosity, and defects, contributing to better overall aesthetics and functionality of the manufactured parts.
- Reduced Thermal Distortion: Beam shaping techniques can be used to control the heat input during the additive manufacturing process. This helps in minimizing thermal distortion, warping, and residual stresses within the fabricated parts. The ability to manage thermal effects leads to improved dimensional accuracy and part stability.
- Increased Build Speed: Beam shaping can optimize the laser beam’s intensity distribution and scan strategies, enabling faster build speeds without compromising part quality. This results in increased productivity and shorter production lead times.
- Versatility in Material Selection: Beam shaping allows for flexibility in using a wide range of materials for additive manufacturing. By adjusting the beam parameters, it becomes possible to process different material types and compositions, expanding the application possibilities of laser additive manufacturing.
“Additive Manufacturing” is a term that encompasses many different techniques and processes. In this application description we outline just two of the laser based additive manufacturing processes for making (or repairing) metal components: (i) Selective Laser Melting; and (ii) Laser Cladding.
Selective laser melting is an innovative manufacturing process that utilises laser beams to create complex three-dimensional metal components. The process of laser additive manufacturing begins with a digital 3D model of the desired object. This model is then sliced into thin cross-sectional layers, which serve as the basis for building the component layer by layer. The machine to additively build the component includes (i) a means of creating a flat powder bed of metal particles; (ii) a wide field of view scan lens; (iii) a high speed 2D or 3D scanner; (iv) a single mode fiber laser, typically 500W to 1kW. As the laser beam scans across the powder bed, it selectively melts or fuses the powder particles, solidifying them to form a solid layer. Fresh powder is applied and this cycle is repeated layer by layer until the complete component is formed. The precise control over the laser beam enables the creation of complex geometries and intricate internal structures that are difficult to achieve using traditional manufacturing methods.
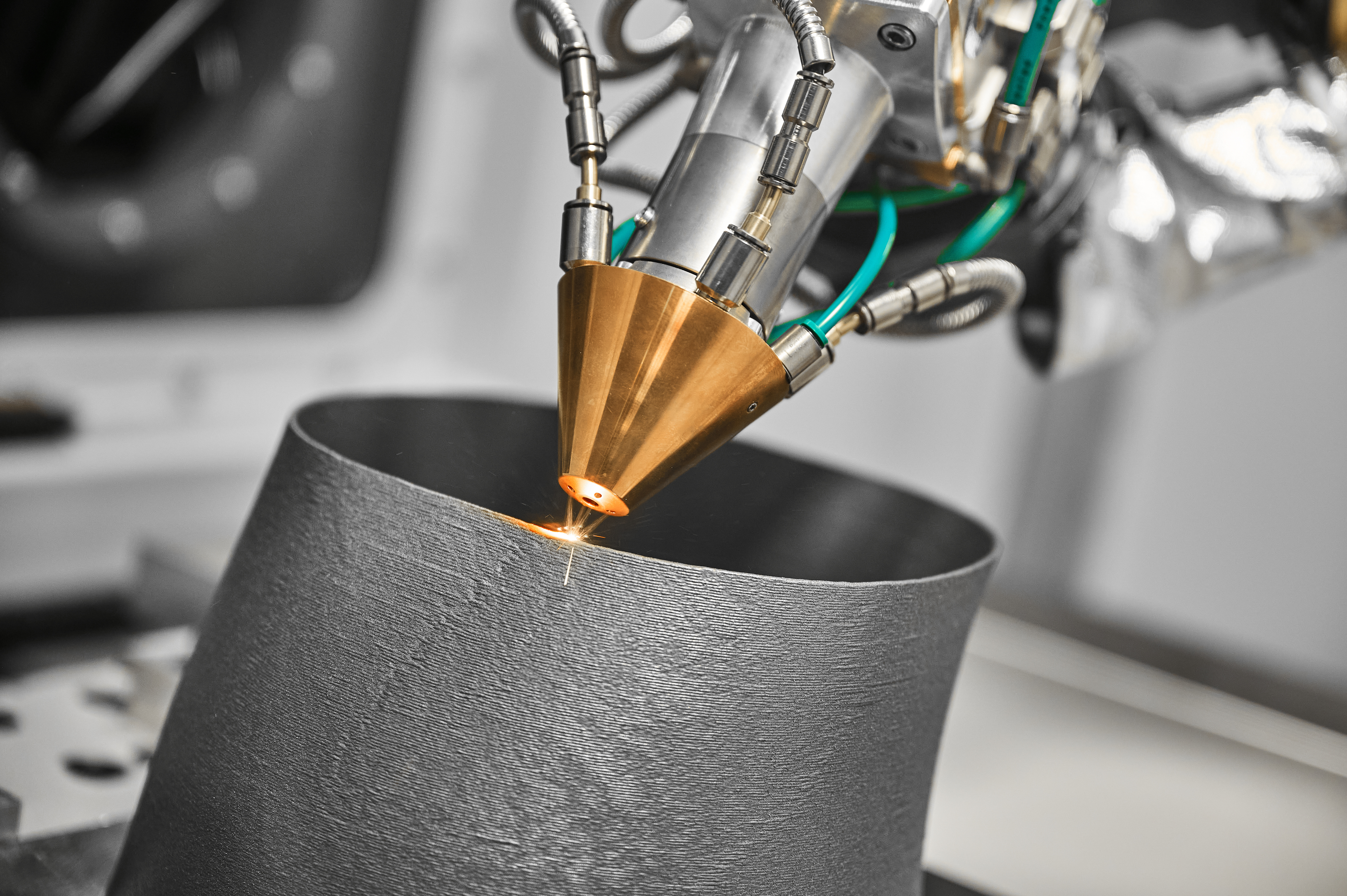